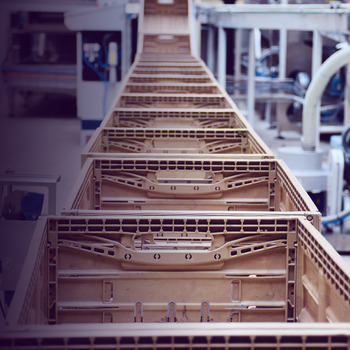
welcome MES
We designed and developed a complete new Manufacturing Execution System (MES) for a publicly listed retail chain with over 8000 stores worldwide and several proprietary production locations. With the implementation of this specific MES, the production facility in Portugal has gained better control over the manufacturing process.
challengechallenge
Developing a completely new customized MES, including the control of conveyor belts and integration with warehouse and order software.
progress
A new user-friendly MES, following the latest technical standards. With enhanced capabilities for new functionalities, the system is future-proof.
impact
Improved production capacity, reduced manual intervention, simplified line and workstation configuration, and enhanced final product quality
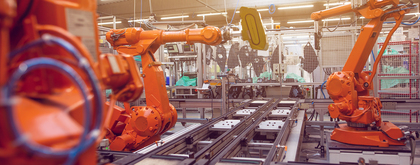
challenge
In a factory, it is essential to maximize production capacity. With various production locations across Europe, this retail chain had one location operating on an outdated Manufacturing Execution System (MES). To gain control over the production process and enhance the quality of the output at the production facility in Portugal, a new MES was necessary.
SST was tasked with the challenge of developing a customized MES, tailored to the factory's operations. This involved not only creating the software for the production line but also ensuring seamless integration with the new warehouse and order software SAP, through SAP PI. Concurrently with the development of the new MES, the customer was implementing SAP SAP EWM & SAP ECC. This made the collection of the appropriate master data and its enrichment a challenging process.
progress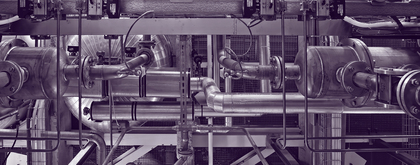
progress
The new MES we have developed, along with the conveyor system and integration with SAP, establishes control over the quality of the production process. There is greater overview of the over 40 parameters of an order before it enters the factory. Additionally, an order can be meticulously tracked throughout the entire production process using sensors and scanners, and extra checks can be incorporated. Any re-routing of orders can now easily be executed.
To enable a suitable MES and effective integration with SAP, we collaborated closely with the client, the factory employees, and other SAP development teams. Using a detailed architecture, we applied an agile development process with continuous testing, feedback and refinements. We also conducted regular on-site testing with the production line hardware. Setting up the test days alongside the ongoing production process was also part of our responsibilities. This yielded valuable insights that facilitated the smooth launch of the MES.
impact20,000
Over 20,000 orders are produced at the production location each week.
5
The MES is integrated with 5 other systems.
50
The project team consisted of 50 individuals.
4
Java, Javascript, Python, and Beckhoff PLC software.
60
Daily, 60 individuals work with the developed systems.
8
A total of 8 applications have been developed.
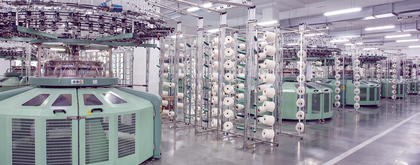
impact
Thanks to the new MES and integration with SAP, the production facility in Portugal now has a better grip on the production process. As a result, specific order types can be distributed more efficiently across the factory and directed to the appropriate machines and workstations. The conveyor system has been optimized for greater intelligence, and it's now also easier to remove hardware from the production line for troubleshooting, without negatively impacting production. The efficient distribution of orders and smarter hardware integration have led to optimal utilization of production capacity and improved quality of the end product.
servicesSST services in this case study
team MES
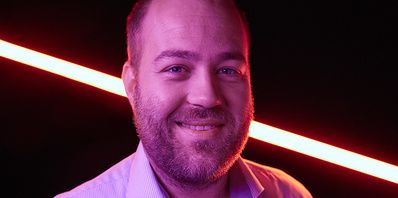
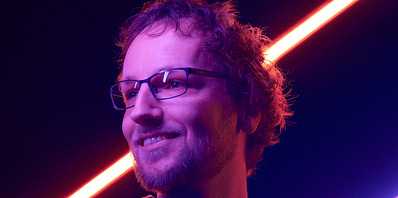
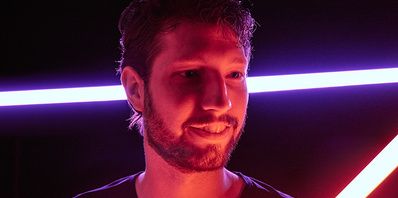
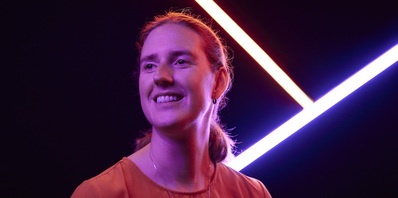
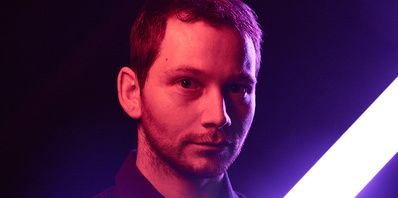
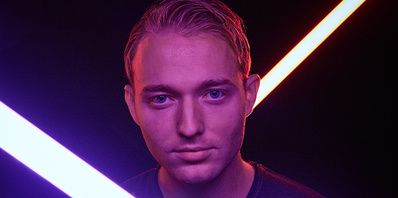
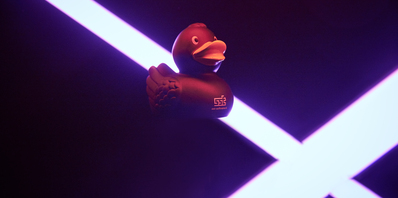
welcome solution
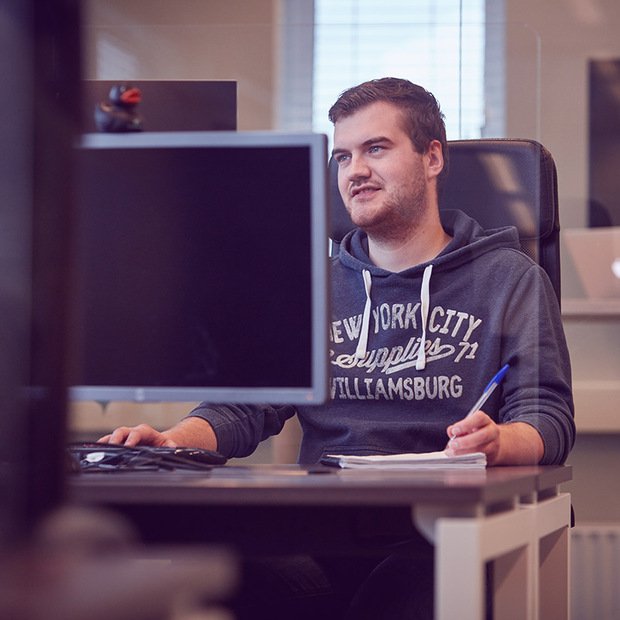